Hemp spells affordable housing for Native American community
The Lower Sioux Indian Community in Morton, Minnesota, has become the first in the country to create a fully vertically integrated “seed-to-wall” program using industrial hemp — addressing a critical shortage of affordable housing on its reservation.
Prompted by U.S. Census Bureau data indicating the need for 200 new homes by 2030, the Lower Sioux Housing Authority turned to an innovative and eco-conscious solution known as hempcrete.
The plant-based building material — a mix of hemp hurd, lime and water — is non-toxic, mold-resistant, biodegradable and highly energy efficient.
Over the past two years, a small team of four tribal members has built homes using hempcrete — laying the foundation for a program that not only provides shelter but could spark housing affordability initiatives in indigenous and underserved communities nationwide.
Community-driven vision
“I guess we started growing hemp in 2016, and there was always an end goal to build homes using hemp,” said Danny Desjarlais, industrial hemp construction project manager for the Lower Sioux Indian Community. “Everything has been a long time in the making here, and a lot of people have put the work in to make it happen.”
That process culminated in June 2023 when construction began on the first hempcrete home.
“We’re not building these big, elaborate, fancy houses for rich people,” Desjarlais said. “We’ve just been making low-budget homes with with way better material. It’s going to last way longer, and it’s way healthier for the people living in them.”
Recognized innovation
The initiative recently earned national recognition as a finalist for the 2025 Ivory Prize for Housing Affordability.
The award, sponsored by Ivory Innovations — a nonprofit housed at the University of Utah’s David Eccles School of Business — honors pioneering approaches to solving the housing crisis.
“Danny has brought a lot of elements together that have helped make this project successful,” said Clark Ivory, CEO of Ivory Innovations and Utah homebuilder Ivory Homes. “I like that he’s targeting affordable, workforces homes and giving people jobs. There’s some limitations right now with scalability, but I’m excited to see what they can do.
“I know they’ve been looking at the Minneapolis market. It will be so cool to see them implement this model outside the reservation and see how it all works.”
Lower Sioux’s approach stands out not only for its environmental merits but also for its replicability.
“We’re just four guys here doing it,” Desjarlais said. “I think we just need to get the word out there more and get more communities doing this to really make it more impactful.”
Real affordability — not just a buzzword
Desjarlais emphasized that the term “affordable housing” often rings hollow.
“Is affordable housing even affordable?” he asked. “Most of the affordable housing I’ve seen, these people can’t even afford to live in it, because it’s poorly insulated. They’re going to (need to choose between buying) groceries, or they’re going to pay their heating bill.”
In contrast, hempcrete homes built in the Lower Sioux Community reportedly offer up to 70% energy savings — potentially cutting heating costs by $4,000 to $5,000 annually.
In one extreme case last winter, a hempcrete house maintained 59 degrees indoors overnight despite subzero temperatures — and without a working furnace.
“We only had this solar furnace where it only attracted the heat during the daytime, and the hemp held that heat in all night long,” Desjarlais said.
Beyond economics, Desjarlais highlighted the health benefits of natural materials like hemp, contrasting them with traditional construction filled with plastics.
“Everything you’d pull out of a hempcrete home, you can either grind it up and put it into your next hempcrete mixes, or put it right into the soil,” he said. “It’s actually good for the soil.”
One of the group’s hempcrete projects involved renovating the oldest home on the reservation. Instead of demolishing the structure, the crew replaced interior walls with hempcrete — preserving the building while dramatically improving its longevity and health profile.
Desjarlais posed a crucial question to fellow tribal and non-tribal communities:
“Are we going to just build the same way that we did already, and then hand this problem down to our kids in 30 or 40 years? Or are we going to try and build homes that will last for generations to come?” he said.
Overcoming regulatory barriers
The team’s tribal sovereignty allowed them to bypass state building codes. But outside of reservation land, other builders faced red tape.
That’s changing. This month, Minnesota became the first state in the U.S. to adopt hempcrete into its building code — an effort Desjarlais helped lead.
“This is going to open the doors here in the state of Minnesota for us and anybody else that wants to build with with hempcrete off of the reservation,” he said. “Then it’s also going to open it for other states to start doing the same thing and just following suit with what we did. I’ve already started reaching out to all of the other states around here.”
Desjarlais also serves as a regional leader for the U.S. Hemp Building Association.
“My region is Minnesota, North Dakota, South Dakota, Illinois, Iowa, Michigan, Nebraska,” he said. “I’ve been reaching out to all of the builders in those states and finding out who their building officials are and trying to get them to push it through at their state levels as well.”
Ivory said he hopes the recent action in Minnesota, as well as similar measures designed to ease the path to affordable housing construction, carry over to more states.
“The U.S. has got to simplify the way we get everything approved,” he said. “You know, our building codes are fairly complicated and vary tremendously from municipality to municipality, not just state to state, and that makes it a little bit complicated.
“I love what (Desjarlais) is doing. I think it’s very it’s a sustainable product, and that we can grow (hemp) and replace it — and just keep doing it again and again and again every year.”
Categories
Recent Posts
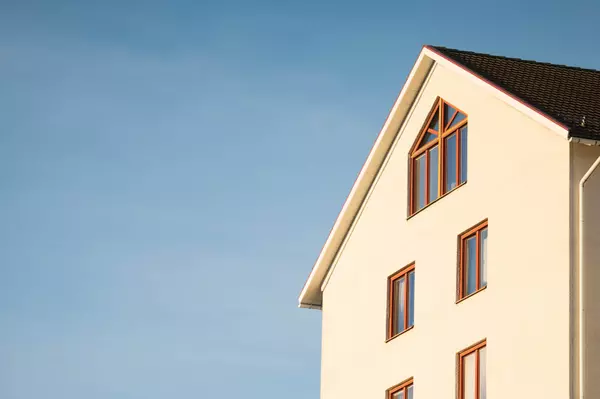

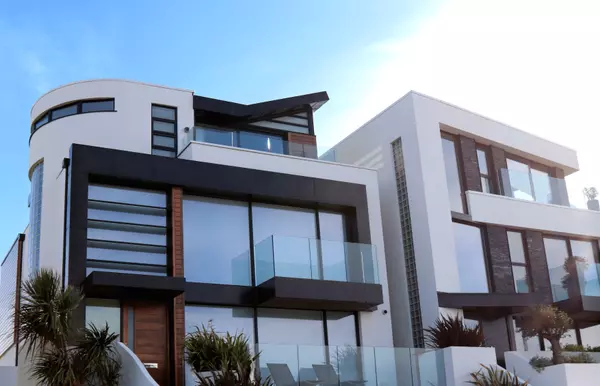
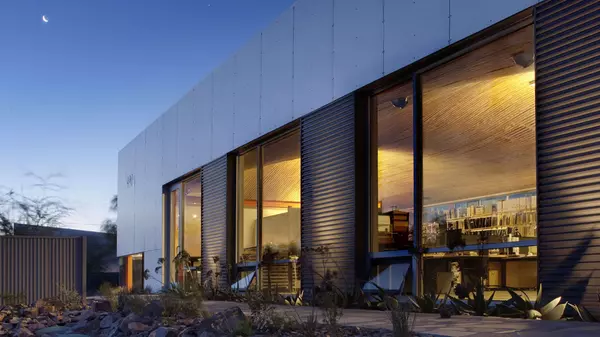
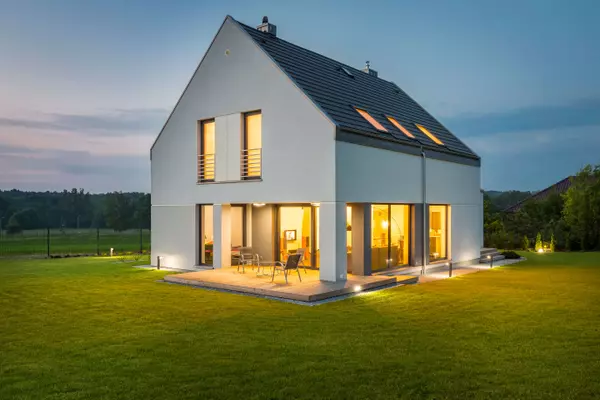
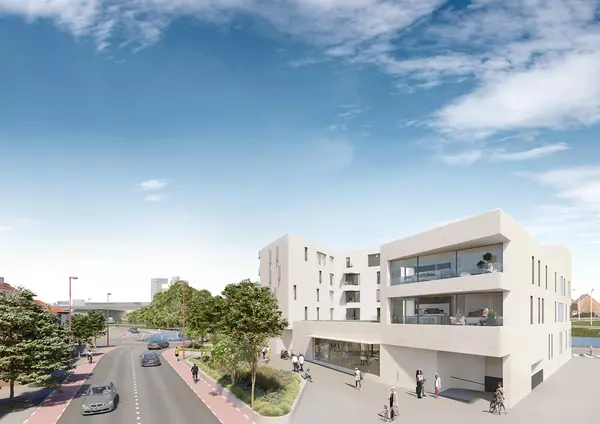
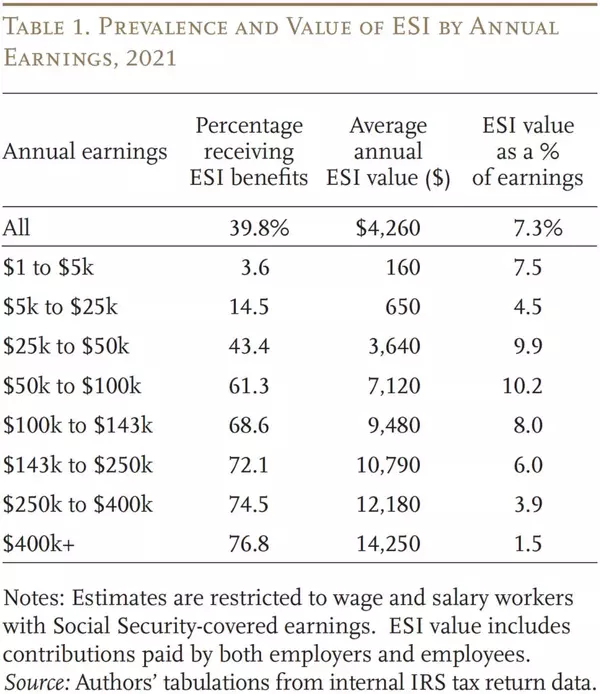
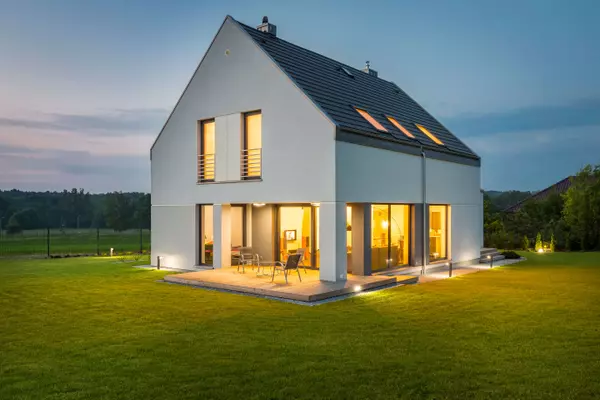

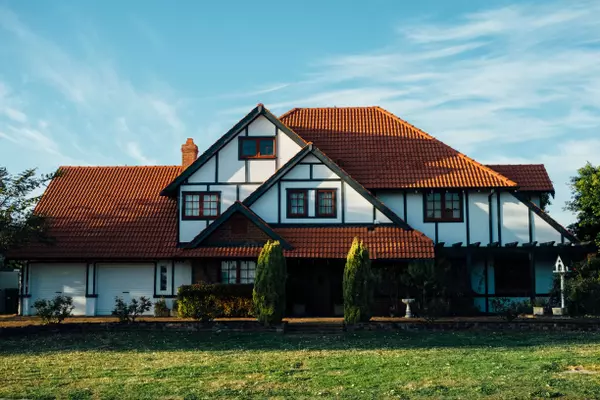